While the automotive industry has achieved drastic mechanical and technological advancement throughout history, there’s one component that all cars with combustible engines have in common: the ignition system.
Knowing how the different types of ignition system work and their advantages and disadvantages is useful in choosing the right spark plug that works most effectively given the performance requirements of the ignition system.
Although almost every major component of a car has undergone improvements through the years, the basic principles of the ignition system have not changed in nearly a century.
In essence, it takes the electrical voltage from the battery, converts it to a much higher voltage, then transfers this electric current to the engine’s combustion chamber and ignites the compressed mixture of fuel and air to create combustion. This combustion generates the energy needed to run your car.
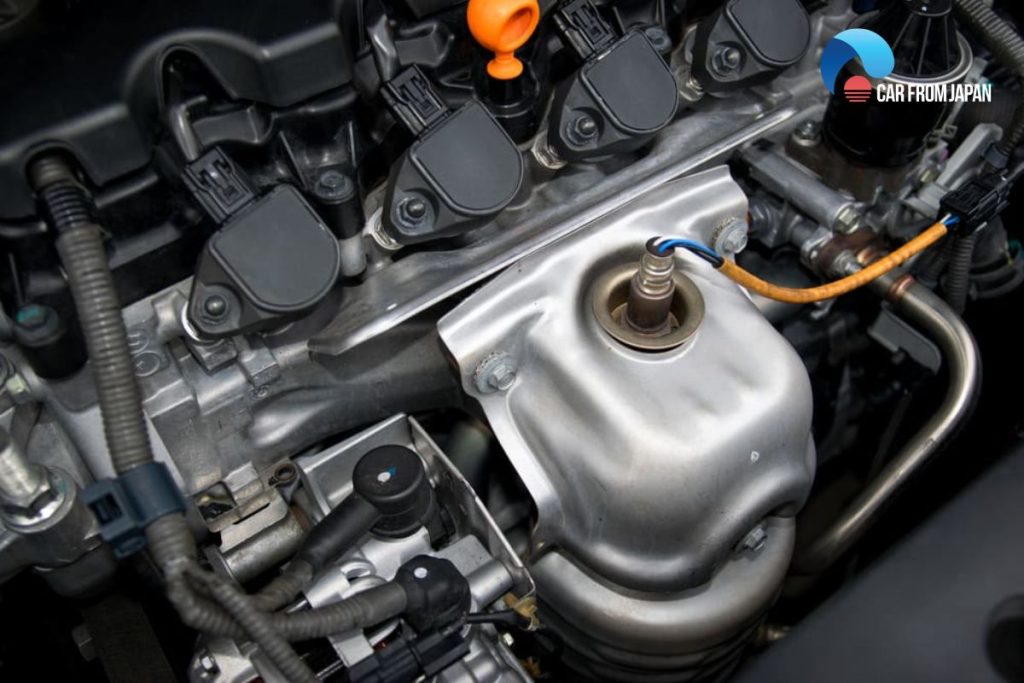
That said, the method by which the spark is created and distributed has greatly improved thanks to technological advancements.
Currently, there are four types of ignition systems used in most cars and trucks, by order of invention: conventional breaker-point (mechanical) ignitions, high energy (electronic) ignitions, distributor-less (waste spark) ignition, and coil-on-plug ignitions.
Breaker-point (mechanical) ignitions and high energy (electronic) ignitions are distributor-based ignitions, so another way to categorize them is by three broader ignition systems types: distributor-based, distributorless, and coil-on-plug systems.
In this comprehensive guide, we will dive into how each system works, as well as the resulting advantages and disadvantages of each, regarding what it means for your engine’s performance and maintenance requirements.
What Does The Ignition System Do?
When you put your key in your vehicle’s ignition and turn, your engine starts and continues running. Have you ever wondered about the whole process that happens behind such a simple action?
Let’s return to Engine 101: Your engine produces power to run your car by creating combustion, or explosion, inside its combustion chamber, hence the name “internal combustion engine”.
To generate such combustion, the ignition system plays a major role: your spark plugs supply the electrical spark that ignites the air and fuel mixture that is fed into the combustion chamber.
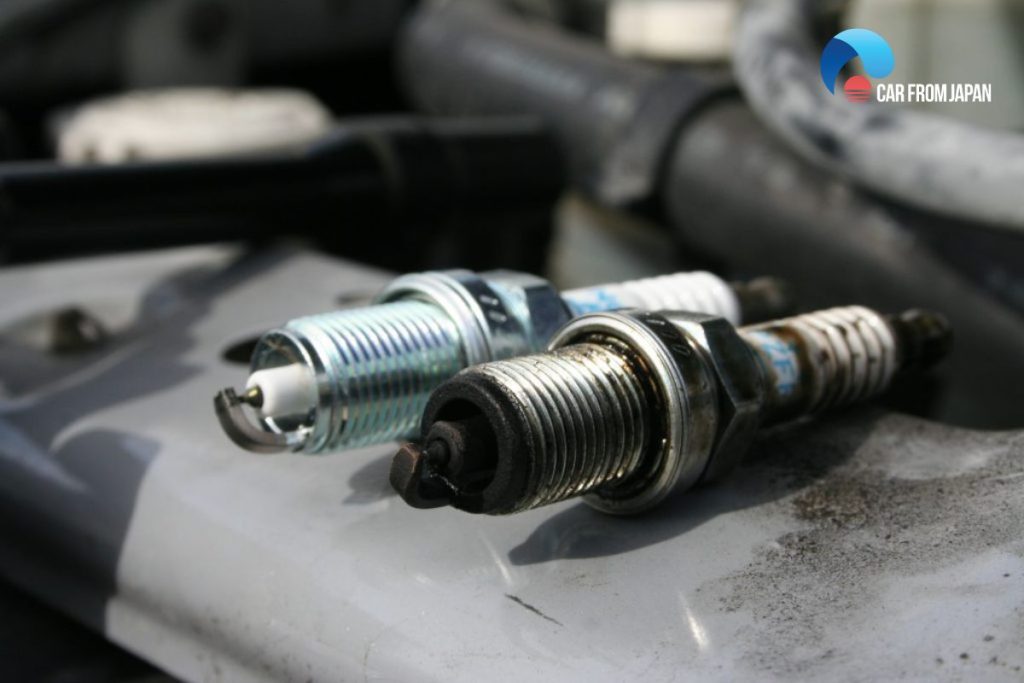
For the ignition system to operate properly, it must be able to accomplish two tasks effectively and accurately at the same time.
Create A Strong, Hot Enough Spark
The first task is to create a strong spark that can jump across the spark plug’s gap. In other words, the ignition system needs to increase the voltage from the battery’s 12 volts to at least 20,000 volts, which is required to ignite the compressed air and fuel mixture in the combustion chamber to create an energy-generating explosion.
To achieve such a huge surge in voltage, the ignition systems in all cars, except diesel-powered models, use an ignition coil consisting of two coils of wire wrapped around an iron core, known as the primary winding and the secondary winding. The ignition coil acts as an electrical power transformer.
The goal of the ignition coil is to create an electromagnet by running the 12 volts supplied by the battery through the primary winding.
When the vehicle’s ignition system triggering switch turns off the power to the ignition coil, the magnetic field collapses. As it does, the secondary winding captures the collapsing magnetic field from the primary winding and converts it into 15,000 to 25,000 volts.
It then supplies this voltage to the spark plug, thereby creating combustion in the engine’s combustion chamber, thus creating energy to start and run your vehicle’s engine.
For the necessary spark to occur, the converted voltage delivered to the spark plug must be in the range of 20,000 and 50,000 volts.
Read More: Types Of Spark Plugs And Their Functions
Fire The Spark At The Right Time
At the same time, the ignition system’s other important role is to ensure that the spark must fire at just the right moment during the compression stroke to maximize the power generated from the ignited air and fuel mixture.
In other words, sufficient voltage must be delivered to the correct cylinder at the precise time and this must be done frequently.
All components to work precisely and harmoniously for your engine to achieve optimal performance. Even the slightest error in timing in any single part will result in engine performance issues, and if prolonged, might even cause permanent damage.
The ignition system must provide sufficient spark at the right cylinder. To ensure accurate spark timing, engineers have used several methods, which have evolved over the years.
The early ignition systems used fully mechanical distributors to control spark timing, followed by hybrid distributors equipped with solid-state switches and the engine control module (ECM), essentially a type of simple-process computer, to distribute the electrical power to each cylinder.
What came after to counter the disadvantages of these early distributors was 100-percent electronic ignition systems, the first of which was a distributor-less ignition system, where the distributor was eliminated.
The latest invention, coil-on-plug ignition systems, was able to significantly improve spark timing by using an improved ignition coil that packs a much bigger wallop and generates a much hotter spark.
What Each Component of The Ignition System Does
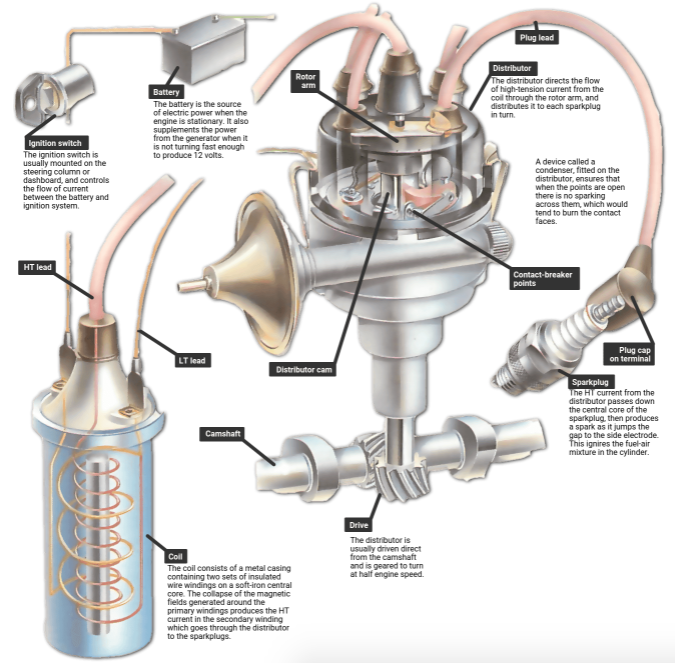
Battery
When the engine is running, it also runs the alternator which generates electricity to recharge the battery. The battery in your car stores electricity and dissipates it as direct current.
The battery supplies twelve volts of direct current. However, in order to achieve a spark for combustion to occur, there needs to be between 20,000 to 50,000 volts at the spark plug. To enable such a considerable increase in voltage, you need the ignition coil.
Ignition Coil
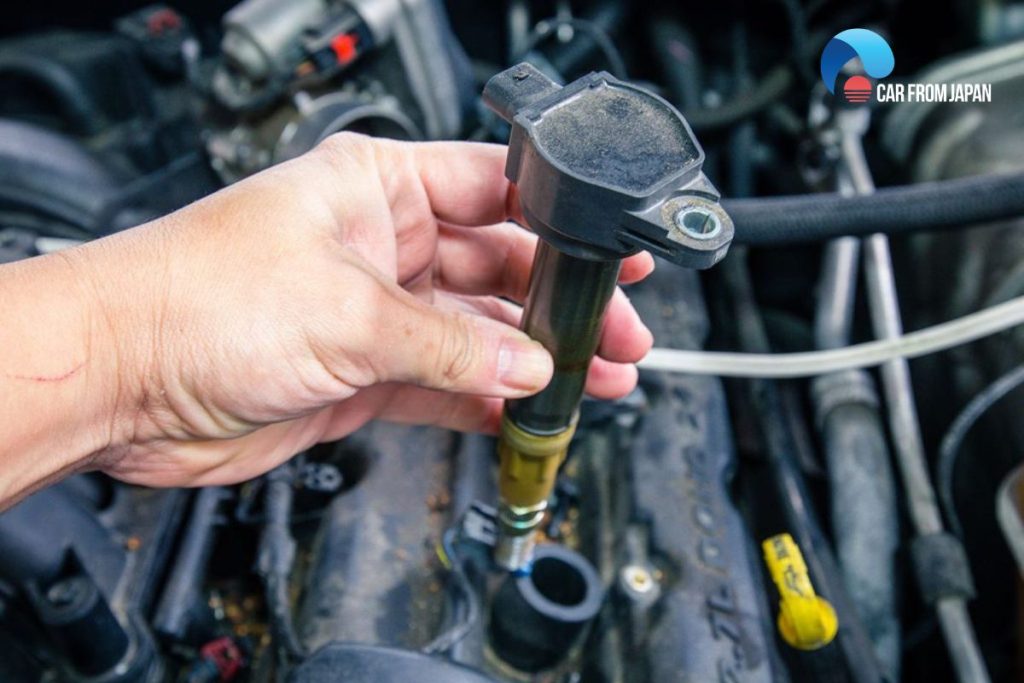
The ignition coil acts as an electrical power transformer. The earliest mechanical ignition systems rely on one coil to convert the low voltage from the battery to the high voltage needed by the spark plugs.
The ignition coil’s electrical transforming works on a principle called magnetic induction. In a traditional transformer, the primary coil receives power, that is direct current from the batteries. However, this charge through the primary coil is periodically disrupted.
This disruption is caused by the distributor in the early distributor-based ignition systems, and by a computer to achieve more precise timing in later ignition systems. The distributor’s job will be discussed further below.
The voltage in the primary coil produces a magnetic field. The periodical disruption to the current that the primary coil receives causes the magnetic field produced by the primary coil to constantly collapse.
Such big movements of the primary coil’s magnetic field cause the secondary coil to create one burst of high-voltage energy at a time.
How high the voltage created by the secondary coil is depends on the ratio of the number of turns in the primary coil to the number of turns in the secondary coil.
If the secondary coil has twice as many turns as the primary coil, the output voltage will be twice the input voltage.
Thus, to increase the voltage from 12 volts to at least 20,000 volts that the spark plugs need, in a car’s ignition coil, the secondary coil has tens of thousands of times as many turns as the primary coil.
Distributor
Here’s how the distributor creates the aforementioned periodic, discrete charges supplied to the primary ignition coil. The distributor contains a “breaker point” that grounds the primary coil’s circuit.
This point is connected to the ground by a lever. The lever gets moved by a cam connected to the distributor shaft. That opens the primary coil circuit and causes the collapse that triggers the high voltage bursts in the secondary coil.
In addition, while the battery and ignition coil provide the power, the distributor does an important job, of determining precisely where and when that power goes to each spark plug.
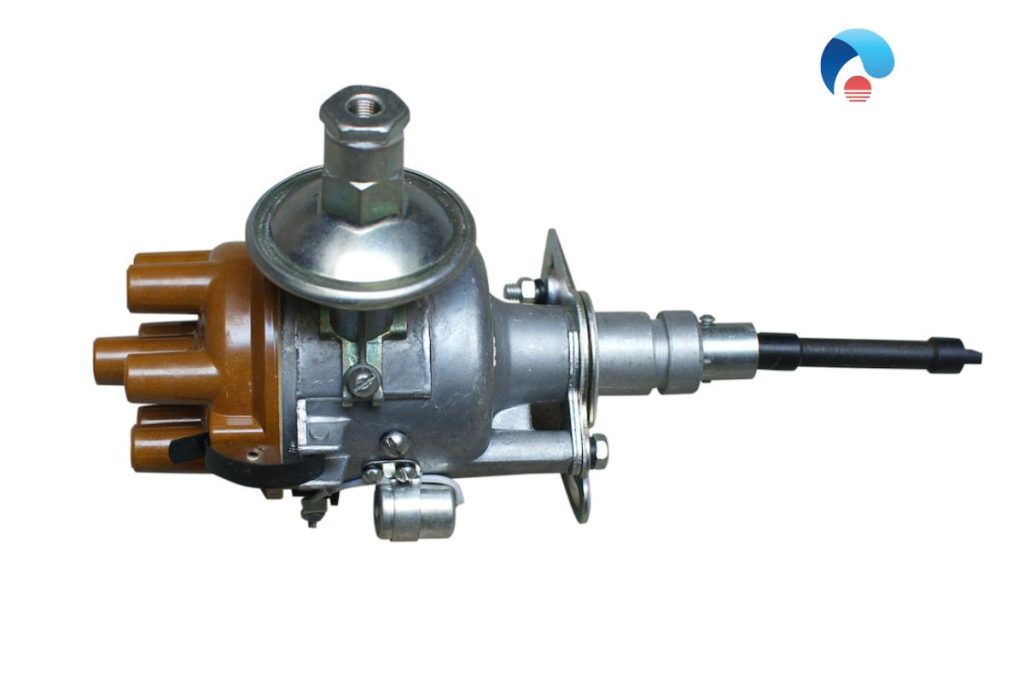
The distributor contains many parts, the most important of which include a rotor that spins in time with the engine, and several “contacts” mounted to the distributor cap. Electric current from the ignition coil is supplied to the rotor.
The rotor spins and when the end of the rotor approaches one of the contacts, electricity arcs to that contact. From there, the power travels down a spark plug wire to the associated spark plug, thus timing the charge to each spark plug.
Spark Plugs and Their Wires
The spark plug wires, also called ignition wires, are insulated wires that carry the power to the spark plugs so that the spark plugs can finally create the spark that causes combustion.
The spark plug consists of an insulated ceramic body with a conductive metal central core at the center.
There is a gap between this metal central core and the tip of the electrode that grounds to the metal base of the spark plug. Electricity arcs or jumps across that gap, causing the spark.
How Important The Ignition System Is
The takeaway is that without the ignition system working properly and precisely, your car may have trouble starting or may not run at all.
Worn spark plugs and faulty components in the ignition system will affect your engine’s performance, creating a wide range of engine problems including difficult starting, misfiring, lack of power, poor fuel economy, and even permanent damage if problems are not addressed in time.
Also, note that these engine problems caused by faulty ignition systems can damage other critical components in your vehicle.
Therefore, regular maintenance of your ignition system is essential in making sure your engine’s optimal performance and thus smooth and safe driving. Then how regular is enough?
At least once a year, you must perform a visual inspection of your ignition system components to check for signs of wear or failure, then replace them at once if required.
Regarding your spark plugs, make sure to inspect and replace them at the interval recommended by your vehicle’s manufacturer.
Again, given how important the ignition system is, preventive maintenance is key to maximizing your engine’s performance and lifespan.
Read More: Should I Replace All Ignition Coils At Once?
Watch more:
Understanding About 4 Types Of Ignition System
1 Distributor-Based Breaker-Point Ignition (Mechanical)
History
The oldest type is the conventional breaker-point ignition system, which sometimes is also called a mechanical ignition system. It has been used since the early days of the automobile industry, especially through the 1970s.
It is one of the two types that use a distributor, called distributor-based systems. Unlike the other three types discussed further below, the breaker-point system is fully mechanical, hence its second name.
A brief description of distributor-based ignition
The first two types of ignition systems, breaker-point system, and electronic system, are both distributor-based, in contrast with the other two distributor-less systems. Thus, let’s learn the basics of how a distributor-based system works.
A distributor is an enclosed rotating shaft that has mechanically timed ignition. The distributor’s main job is to route the secondary, or high voltage, current from the ignition coil to the spark plugs in the correct firing order, and for the correct amount of time.
In the fully mechanical distributor, the distributor connects to the camshaft with gears and gets spun by the camshaft.
Inside, the multi-sided cam on the distributor shaft moves other distributor parts, essentially acting like a mechanical switch that starts and stops the flow of power to the ignition coil.
Once the coil generates enough voltage, it travels to the top of the coil and into the top of the distributor cap.
There, a rotating disc attached to the distributor shaft distributes the electric current to each of the spark plug wires in order. The current travels down the spark plug wires to the spark plugs and causes ignition.
How breaker-point ignition works
A distributor-based breaker-point ignition system has two electrical circuits, the primary and secondary circuits.
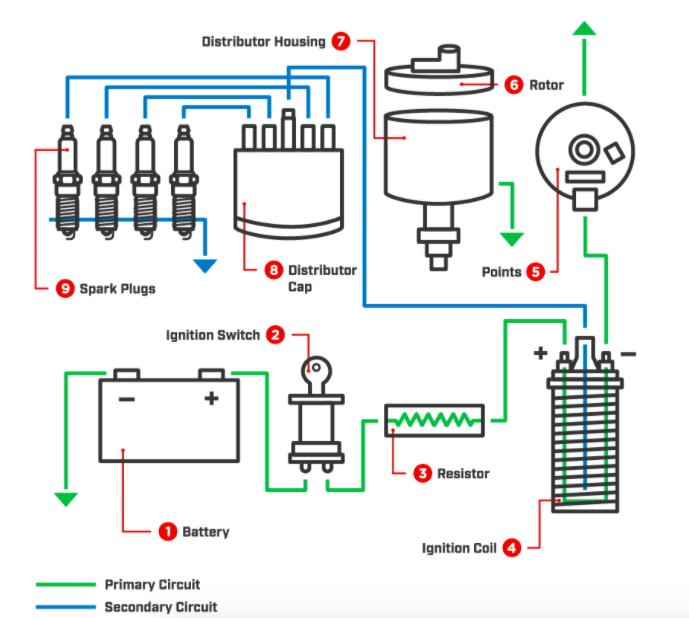
An ignition coil consists of two coils of wire wrapped around an iron core, known as the primary winding, or primary coil, and the secondary winding, or secondary coil.
The primary circuit consists of the primary coil, the “breaker point” and the car’s batteries. It operates only on the battery’s low current and is controlled by the breaker points and the ignition switch.
Meanwhile, the secondary circuit consists of the secondary windings in the coil, the high-tension lead coil wire on external coil distributors, the spark plugs, the spark plug leads, the distributor rotor, and the distributor cap.
When the ignition key is turned on, the primary coil receives low-voltage direct current from the batteries, which runs through the distributor’s breaker points and back to the battery. This current flow forms a magnetic field around the ignition coil.
Now here’s how the “breaker-point” comes into play.
As mentioned above, the distributor contains a “breaker point” that grounds the primary coil’s circuit. This breaker point is connected to the ground by a lever, which gets moved by a cam connected to the distributor shaft.
Thanks to the distributor rotor that rotates in time with the engine, as the engine spins, the distributor shaft cam turns until the high point on the cam causes the breaker points to separate. Instantaneously, this sudden separation stops the current flow through the primary coil.
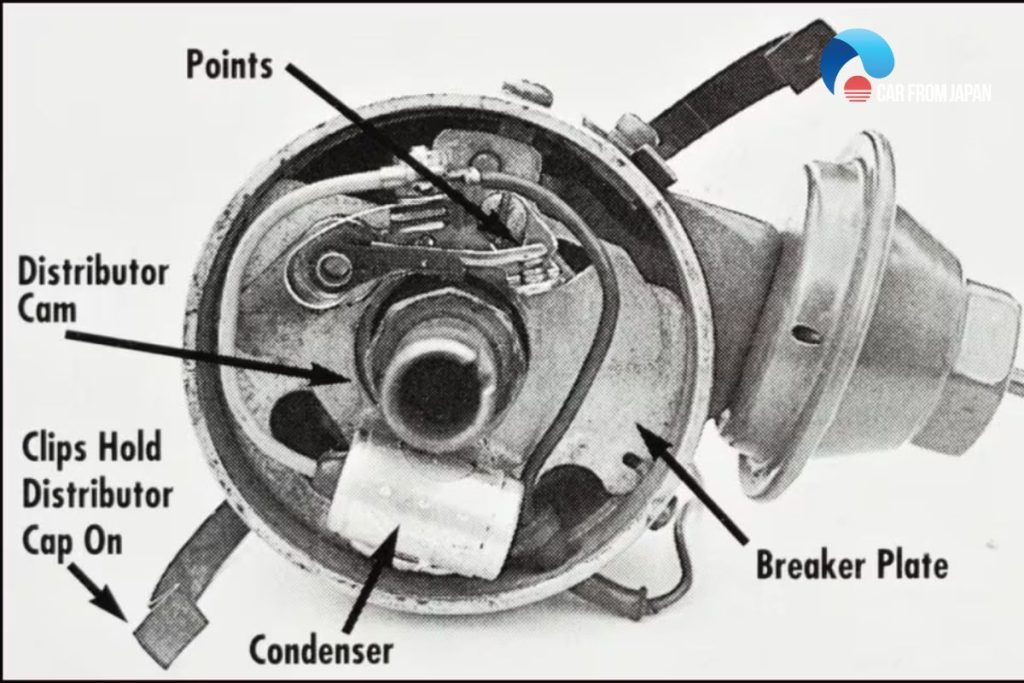
This causes the magnetic field produced by the primary coil to collapse around the coil. The condenser absorbs the energy and prevents electric arcing between the breaker points each time they separate.
Thus in other words, the condenser plays a role in the rapid collapse of the magnetic field, which is required to create a high voltage surge in the secondary coil.
Such sudden and continuous changes in the magnetic field of the primary coil cut through the secondary coil, creating a high voltage surge that’s high enough to jump the gaps between the rotor and the distributor cap terminals, and the gaps between the electrodes of the spark plug.
Assuming the whole system is properly timed, the spark reaches the air-fuel mixture in the designated cylinder at the accurate moment and a combustion is born in that cylinder.
As the distributor continues to rotate in time with the engine, electrical contacts between the rotor and distributor cap terminal are interrupted, stopping the current flow to the secondary coil.
At the same time, the breaker points close again, making the primary circuit complete, and allowing the current to flow again through the primary coil.
This current will again create a magnetic field around the primary coil, which will be made to collapse again, and the cycle is repeated for the next cylinder in the firing order.
It should be noted that in breaker-point systems and the later electronic systems, a single coil, which consists of a primary winding and secondary winding, powers all the cylinders.
This whole “magnetic induction” process takes place approximately 18,000 times per minute at 90 miles per hour.
Breaker-point ignition summary:
Pros
- Easy maintenance: The mechanical nature of these ignition types, as well as the fact that these systems have been around the longest, render them relatively easy to diagnose and repair.
Cons
- Likely to breakdown: However, they consist of a large number of mechanically moving parts, thus also increasing the potential for wear and tear, malfunction and breakdowns.
- Affect engine performance: Such likely deterioration of these ignition systems can decrease the maximum spark energy over time, causing frequent engine problems such as misfires and increased emissions.
2 Distributor-Based Electronic Ignition
History
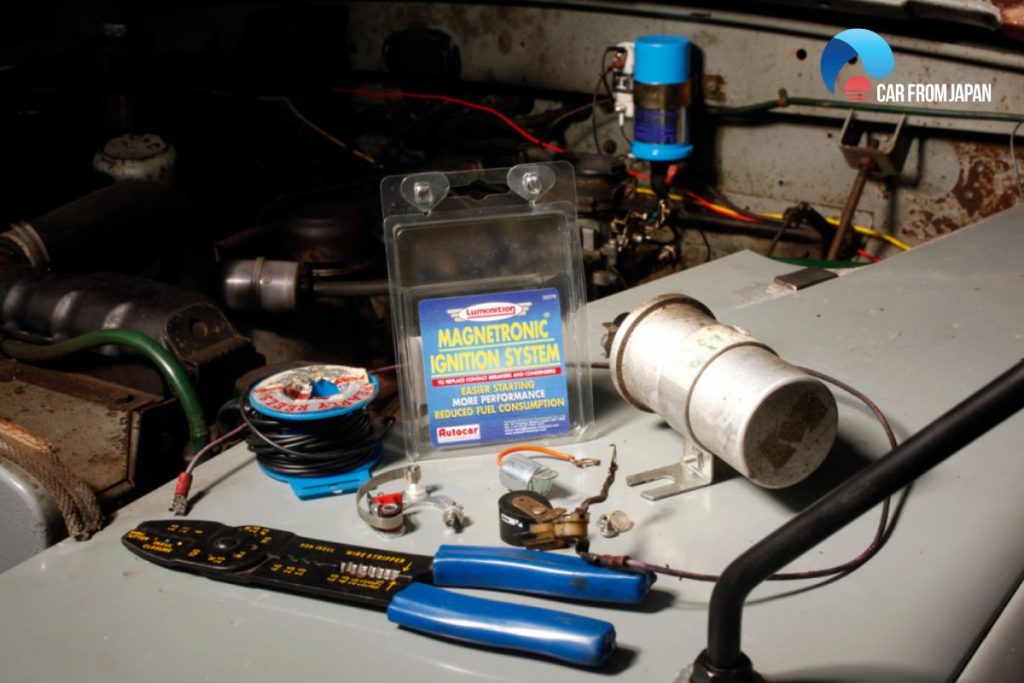
After the fully mechanical breaker-point ignition systems had been around for more than 70 years, the automotive industry was facing the demand for higher mileage, greater reliability and reduced emissions.
Manufacturers came up with a high energy system that relied less on mechanical workings: the electronic ignition system.
The breaker points in earlier systems would break down and mess up spark timing, negatively affecting the engine’s performance and would require replacement as often as every 12,000 miles.
To deal with this shortcoming, the later electronic ignition system still has a distributor, but the breaker points and the condenser have been replaced with a pickup coil that acts as a transistorized switch and an electronic control module that controls the ignition coil to generate high-voltage current.
Compared to the earlier breaker-point ignition system, the use of such an electronic switch for controlled timing means there are fewer moving parts, making these electronic ignition systems relatively easy to diagnose and repair.
They also improve upon the disadvantage of the breaker-point system by creating a consistent, high-voltage spark throughout the life of the engine, meaning fewer engine misfires and reasonable emissions.
These electronic systems still use a conventional distributor cap and distributor rotor to perform the same job of distributing current to the spark plugs (thus they are also distributor-based ignition systems).
Despite having fewer moving parts, the distributor is also exposed to wear and tear and will eventually require replacement — which prompted further improvements in later ignition systems in this regard.
Another limitation of electronic ignition systems is that the ignition timing is yet to be precisely controlled as manufacturers desired, resulting in sluggish acceleration and poor fuel efficiency.
How electronic ignition works
Like early breaker-point ignition systems, electronic systems have two ignition coils and accordingly two circuits, a primary circuit, and a secondary circuit.
The part of the primary circuit from the battery to the battery terminal at the primary coil stays unchanged, as well as the entire secondary circuit.
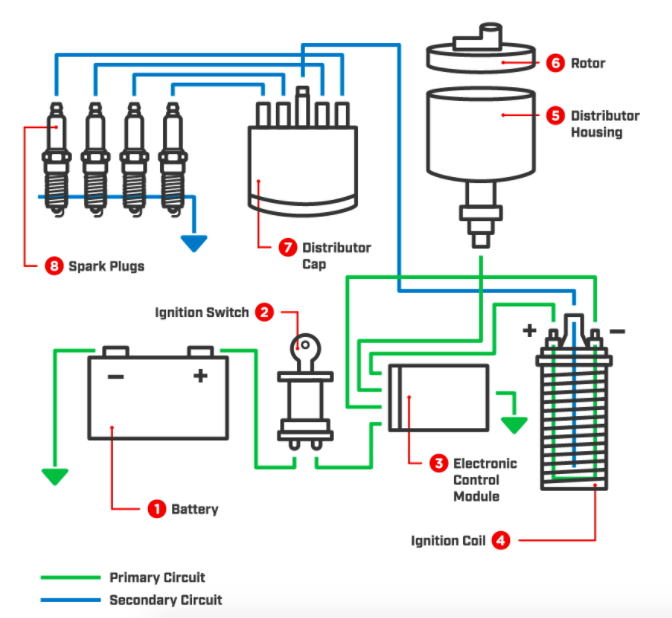
When the ignition switch is turned on, battery low-voltage current runs from the battery through the ignition switch to the primary coil.
Instead of the breaker points in earlier systems, the current is disrupted and turned back on continuously by a component called the armature, which has many “teeth”, as it revolves past the pickup coil, which acts as a sensor.
As each tooth of the armature approaches the pickup coil, it creates a voltage that signals the electronic module to turn off current flow through the primary coil. In essence, this mechanism is quite similar to that in breaker-point systems.
When the current is disrupted, the magnetic field around the primary coil collapses, creating a high voltage spurt in the secondary coil. The electric current now operates on the secondary circuit, which is the same as in a breaker-point system.
A timing circuit in the electronic module will turn the current on again after the primary coil’s magnetic field has collapsed, and the whole process repeats for each cylinder in the firing sequence.
Electronic ignition summary
Pros:
- Less likely to break down: The breaker points and condenser are removed, thus electronic systems have fewer mechanical moving parts, thus are less likely to break down.
- Reliable: Unlike breaker-point ignition systems, electronic systems can generate consistent, high voltage spark throughout the life of the engine, meaning fewer engine misfires and reasonable emissions.
Cons:
- Maintenance: Still, the distributor remains, which is subject to wear and tear and will require replacement, adding to repair costs.
- Timing: Spark timing is exactly precise, resulting in sluggish acceleration and poor fuel economy.
3 Distributor-less Ignition
History
A shortcoming of the electronic ignition systems is that they still have the distributor, which is subject to wear and tear. In addition, the distributor tends to accumulate moisture and cause difficult starting problems.
The distributor also requires engine power to spin, as it gets spun in time with the engine, thus no distributor means less engine drag and increased efficiency.
Manufacturers came up with a solution: to remove the fully mechanical distributor and replace it with solid-state switches that don’t wear out.
Doing so increased reliability, but the solid-state switches still took their marching orders from the distributor shaft, which was still mechanically rotated by the camshaft.
And distributor shafts are subject to wear and tear, and would tend to develop problems after some 120,000 miles.
Any wear and tear always impedes proper spark timing, thus beginning in the early ’80s, manufacturers removed the mechanical distributor altogether to introduce the distributor-less ignition system.
These systems are very different from breaker-point and electronic ignition systems, The ignition coils now sit directly on top of the spark plugs, spark plug wires are eliminated, and the system is fully electronic.
How electronic ignition works
The third types is the distributor-less, also called waste spark ignition system. Instead of a conventional trouble-breeding distributor, this system uses multiple ignition coils: one coil per cylinder or one for each pair of cylinders.
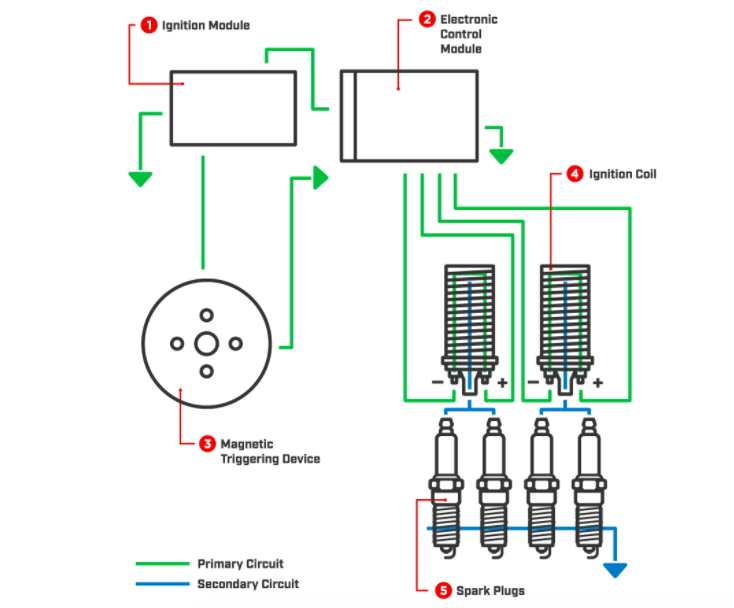
Without the distributor to “distribute” electric current to the spark plugs, the spark plugs are fired directly from the coils. Spark plug timing is controlled by an electronic ignition module and the engine computer.
This system uses engine sensors to determine crankshaft position and camshaft position. These sensors continually monitor the positions of both shafts and deliver that information to the engine computer.
The Crankshaft Position Sensor is mounted at the front of the crankshaft, or near the flywheel on some vehicles, and the Camshaft Position Sensor is mounted near the end of the camshaft.
Based on the two shafts’ position, the electronic ignition module triggers the appropriate ignition coil, which directly fires the associated spark plugs.
This system also uses a “waste spark” for one of the paired cylinders, pairing two pistons that will be at the top dead center at the same time: one at the end of its compression stroke, and the other at the end of its exhaust stroke.
Another major difference compared to its predecessor is that while earlier systems uses a single coil, which consists of a primary winding and a secondary winding, to power all the cylinders in a particular order, distributor-less ignition systems employ a different coil setup.
It uses multiple ignition coil packs, each generating spark for just two cylinders, which means each coil can be turned on for longer.
Therefore, this soil setup is capable of developing a stronger magnetic field of up to 30,000 volts, as well as stronger, hotter spark required to ignite the typical leaner air-fuel mixtures of more modern vehicles.
Each of the spark plugs in these cylinders will fire at the same time using the high voltage from one coil. This allows for more precise ignition timing, thus higher engine efficiency and lower emissions.
Electronic ignition summary
Pros:
- Reliable: Can generate consistent, high voltage throughout the engine’s lifetime.
- Precise spark timing: Since the distributor, which is subject to wear and tear after certain miles, is removed, spark timing can be precisely controlled, thus allowing for lower emissions.
- Less likely to break down: thanks to the lack of moving parts, as the system is now electronic.
Cons:
- More costly maintenance: However, the lack of moving parts also means that it can be much harder to diagnose and is more expensive to repair once a problem breeds than the mechanical ignition systems.
- More expensive parts: Distributorless systems require double platinum spark plugs to facilitate its firing mechanism.
Read More: How To Gap Spark Plugs: Explained In Simple Steps
Coil-On-Plug Ignition
History
The coil-on-plug ignition system has all the advantageous electronic controls developed in the distributor-less systems.
Also, like the distributor-less system, the coil-on-plug system places an ignition coil directly on the top of each spark plug to fire the spark plug directly, hence the name.
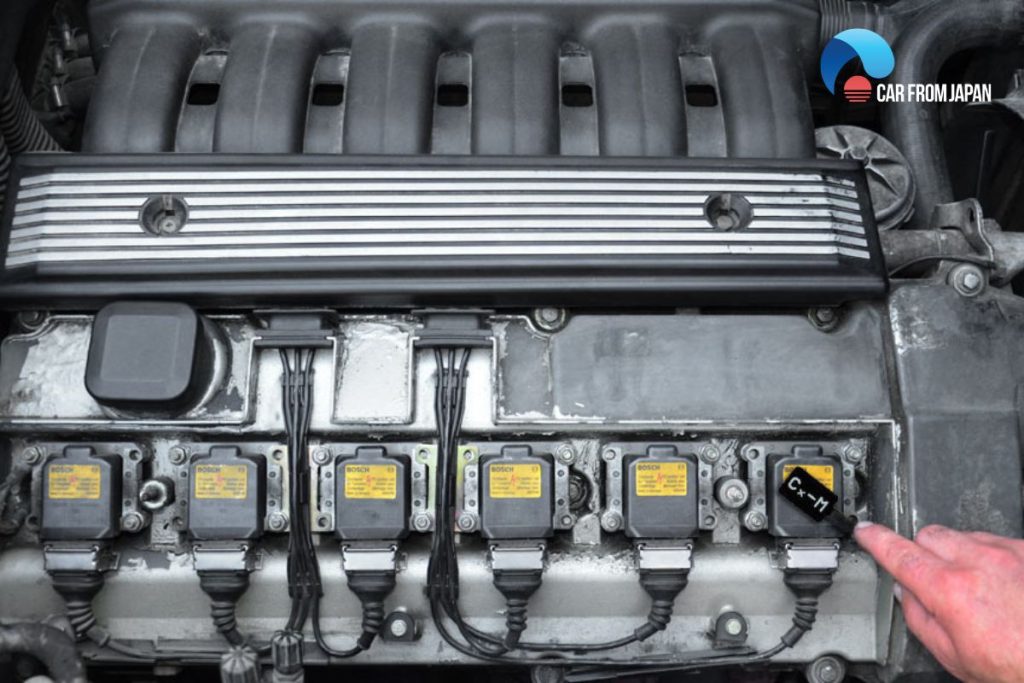
Because each spark plug now has its own dedicated coil that sits right on top for direct firing, high-voltage spark plug wires are completely removed.
This increases the system’s efficiency, since spark plug wires introduce greater loss of amperage and voltage, as well as the possibility of contamination and cross-firing between cables if they become greasy or worn.
Another major improvement here is instead of two cylinders sharing a single coil, each coil now services just one cylinder. This means each coil can be “turned on” for twice as much longer to develop maximum magnetic field.
As a result, coil-on-plug ignition systems can generate between 40,000 and 50,000 volts, compared to up to 30,000 volts in distributor-less systems, and much hotter, stronger sparks to more efficiently burn the leaner air-fuel mixture, thereby maximizing engine’s efficiency.
Now, there are no breaker points, distributors, condensers, and spark plug wires. No moving parts means coil-on-plug ignition systems are less likely to break down, are more reliable and command less frequent repair.
On the downside, it should be noted that the lack of moving parts can make it more difficult to diagnose and more expensive to repair than a traditional system once there is indeed a problem, but as said, repairs are less frequent.
It should also be noted that the ignition coils are now sitting on top of the spark plugs, thus more exposed to damage by degreasers and water during under-hood engine cleaning, so be sure each is wrapped in plastic for protection before any cleaning begins.
How coil-on-plug ignition works
The most sophisticated of all ignitions systems, this system controls spark timing using the Engine Control Unit, based on input from various sensors, to achieve the optimal precision, higher voltage, and stronger, hotter spark.
Similar to the distributor-less systems, coil-on-plug systems use engine sensors to know the shafts’ position.
Based on this information, the Engine Control Unit triggers the appropriate ignition coil, which directly fires the associated spark plugs in the associated cylinder in the firing order.
Coil-on-plug ignition summary
Pros:
- Engine efficiency: Can generate consistent, high voltage and hotter, stronger spark that can efficiently burn the leaner air-fuel mixture in newer vehicles.
- Precise spark timing: This allows for optimal engine efficiency and lower emissions.
- Less frequent repairs: thanks to the lack of moving parts as spark plug wires are now removed.
Cons:
- Repairs: No moving parts means difficult troubleshooting and more expensive repairs.
Final Words
Ignition systems will continue to improve with features that today are unimaginable as technology advancements lead to continued improvements.
Even as they do, all the four types of ignition system are still easy to maintain and repair, and well-suited for the vehicles of their own era.
To learn more about important components in your precious vehicle and how they work, dive into our comprehensive maintenance tips articles.