The task of manufacturing cars and automobiles is incredibly complex, and one that involves a myriad of components and individual processes.
Pressure sensors represent one of the most important (albeit understated) automotive components, while the overall market for this is forecast to grow by a CAGR of 10.3% over the course of the next six years.
So, by 2027, the pressure sensor market will be worth an estimated $24.84 billion, while there remains significant scope for further growth in the longer-term.
In this post, we’ll consider the history of pressure sensors in car production, while asking how they’re applied in this context.
A Brief History of Automotive Pressure Sensors
If you buy a new vehicle in the modern age, you’ll find an electronic engine control module combined with a variety of pressure sensors.
The latter component offers critical input in the form of ‘manifold absolute pressure’ (MAP), which plays a pivotal role in the speed density regime and allows the mass flow of air throughout the engine.
It subsequently enables the flow of fuel and allows for optimal operation, while controlling engine efficiency in an age of increasingly green vehicles.
While the dominant design for contemporary MAP sensors is a micromachined silicon piezoresistive pressure sensor, formative components contained analog signal conditioning circuits.
These were typically built using off-the-shelf and packaged ICs that were mounted on a PCB, with any subsequent adjustments quite cumbersome and completed using laser trimming of a thick film resistor network.
Over time, advances in hybrid circuit technology have laid the foundations for the pressure sensors that we see today, while making these components far more compact and increasingly cost-effective.
The next generation of pressure sensors were known as discrete-analog trimming, which (as the name suggests) was based on discrete as opposed to continuous and retrospective adjustments.
With this type of sensor, fusible links could be opened to make steps in the resistance or current value, although the sensor signal remains firmly in analog firm.
These sensors also utilised two chips to power optimal operation, with modern alternatives integrating the functionality of MAPs into a single one.
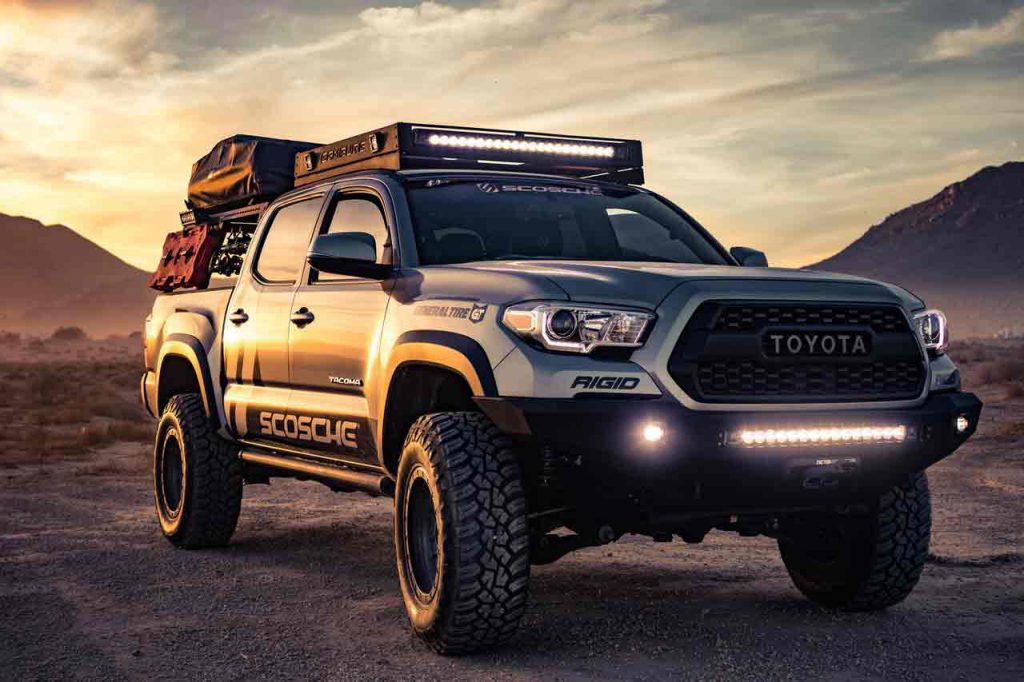
The Most Innovative Applications of Pressure Sensors in Automotive Production
As these sensors have become increasingly compact and sophisticated, they’ve also evolved to perform a wider range of innovative tasks within automotive vehicles.
For example, contemporary MAPs can be used to detect early faults in hydraulic brakes, primarily because they play a key role in creating the sensation and feeling of responsiveness in the pedal beneath your feet.
When combined with in-car systems, modern pressure sensors can also detect the pressure levels that are applied to the brake pedal in real-time and amplify it to make your efforts efficient.
We’ve already touched briefly on how pressure sensors work to optimise the fuel performance in your car, primarily by maximising the mix to match the air pressure.
This function has become increasingly important in the age of energy-efficient and hybrid vehicles, with pressure sensors enabling internal combustion engines to operate at their full potential in a range of different scenarios.
Interestingly, you can purchase a range of pressure sensors for automotive purposes from suppliers such as RS Components, allowing you to create tasks such as cleaning exhaust filters automatically and checking the pressure levels of critical fluids.
Even on a fundamental level, pressure sensors help to power electric door closing on modern cars and can prevent you from catching your fingers in them!
This definitely highlights the wide appeal and huge range of applications for pressure sensors in the automotive space, alongside their incredible evolution over time.